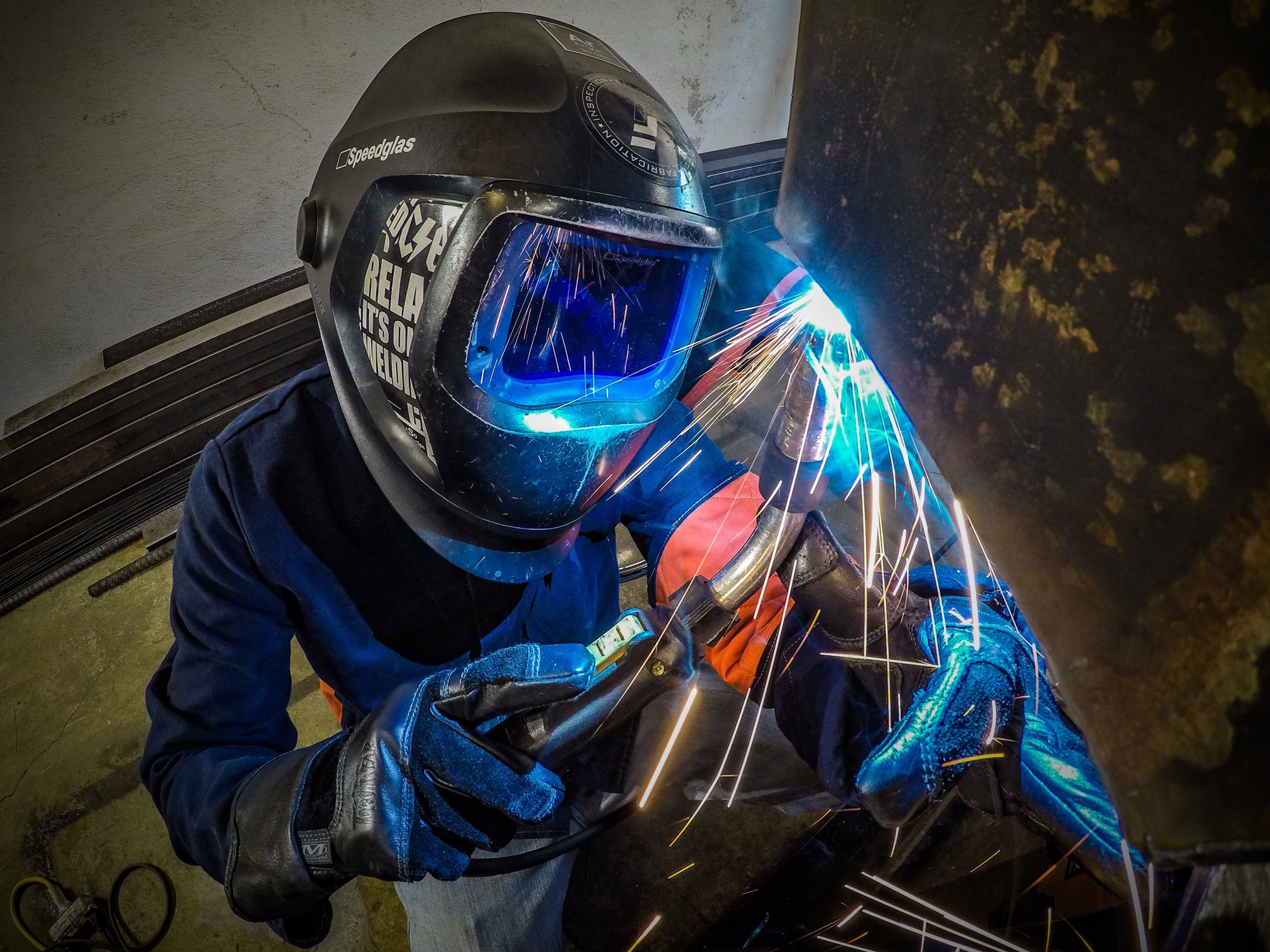
MIG and TIG welding are two of the most common methods of arc welding in which metal electrodes and an inert gas are used to shield the weld area from contamination.
MIG Welding
MIG stands for Metal Inert Gas welding, and the technical name is GMAW, or Gas Metal Arc Welding. In this process, a continuous solid wire electrode is fed through a welding gun along with shielding gas, normally an Argon mix. The materials are joined together when the consumable solid wire connects with a current which creates an “arc" between the weld metal and the base material. Shielding gas is also fed through the welding gun during this process protecting the weld pool from atmospheric oxygen and other contaminants.
In MIG welding, there are four different basic modes to transfer weld metal across the arc to the base material. These transfer modes are Short Circuit, Globular, Spray Arc and Pulsed MIG. We will cover the different transfer modes in a later post.
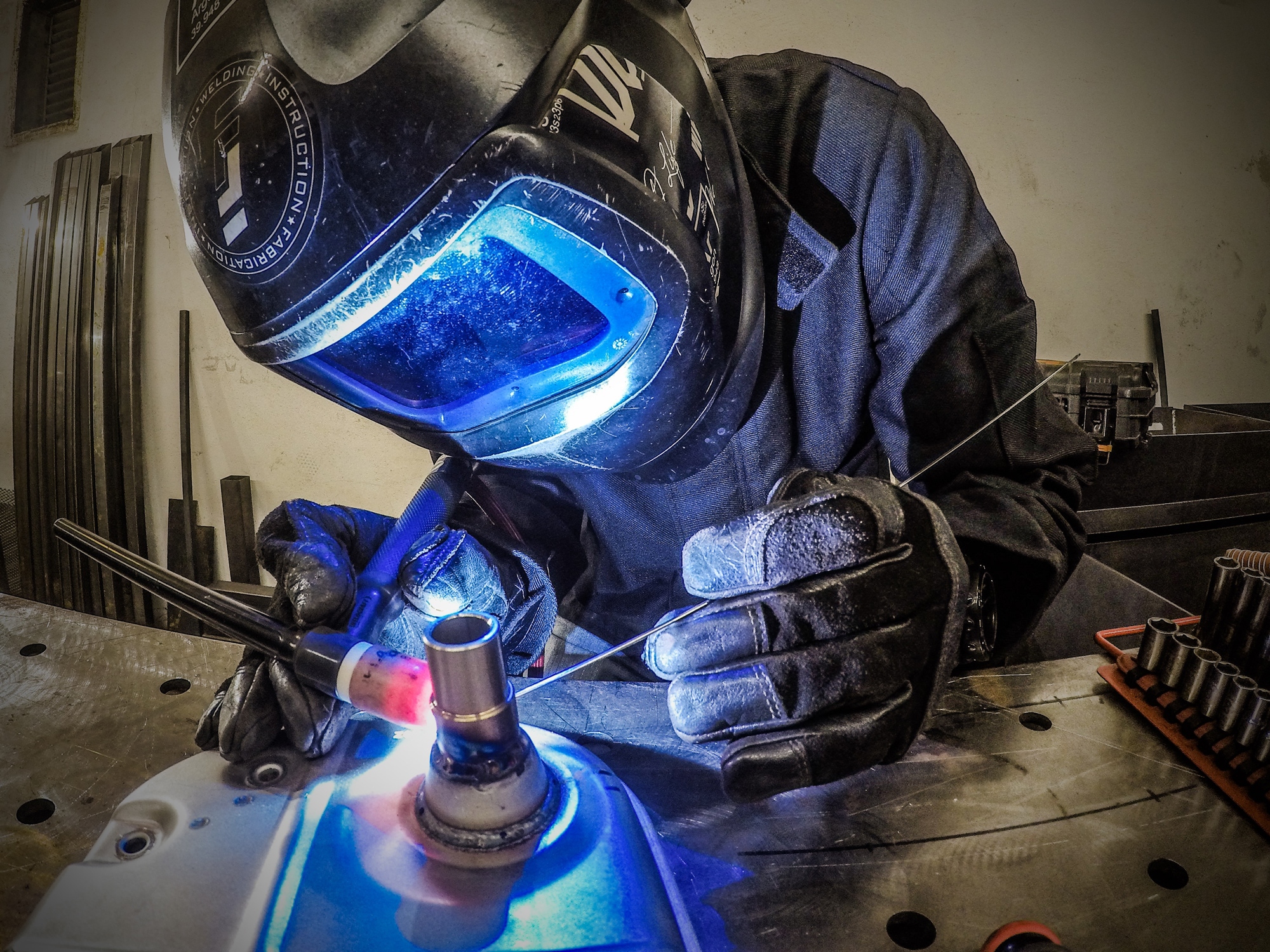
TIG Welding
TIG stands for Tungsten Inert Gas welding. Its technical name is GTAW or Gas Tungsten Arc Welding. Gas tungsten arc welding had its beginnings from an idea by C.L. Coffin to weld in a non-oxidizing gas atmosphere, which he patented in 1890. The concept was further refined in the late 1920s by H.M. Hobart, who used helium for shielding, and P.K. Devers, who used argon. This process was ideal for welding magnesium and also for welding stainless and aluminum. It was perfected in 1941, patented by Meredith, and named Heliarc welding.
Unlike MIG welding, which uses a consumable wire, TIG welding uses a non-consumable tungsten electrode to create the arc and the filler material is added externally to the weld puddle. TIG also uses an inert shielding gas (Argon or an Argon Helium mixture) to protect the weld pool from contamination from atmospheric oxygen and other impurities. TIG welding allows for greater operational control when compared to MIG because you control the amperage (heat source) by foot pedal and manually feed the filler metal. This allows the operator to adjust the heat and filler metal on the fly, therefore controlling the size and contour of the weld. The downside is that TIG welding requires greater skill compared to MIG welding.
So, which method creates the stronger weld?
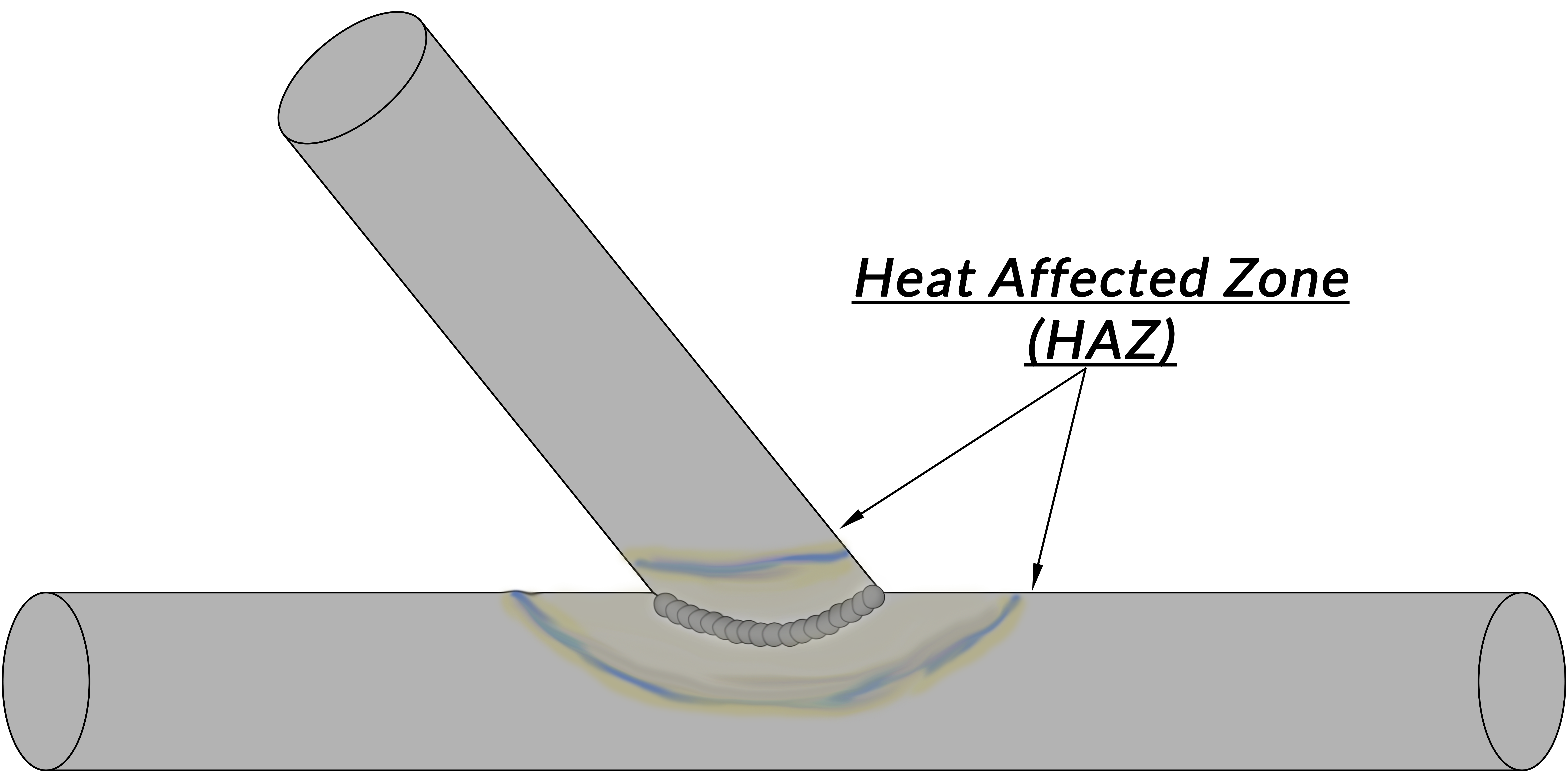
The answer is NEITHER. If you performed tensile strength tests on materials welded in each method, both would net the same weld metal tensile strength, assuming there were no weld defects in either weld.
The difference in welds comes down the skill of the operator. Heat inputs are a major factor in the tensile strength of the weld. The higher the heat input, the wider the Heat Affected Zone (HAZ), and that can diminish the strength of the material. It is a common misconception that “the hotter, the better” because of better penetration, but the increased HAZ can diminish the strength values. This is why TIG is often considered the better method, as better operational control allows you to control all of the variables.
We would like to credit Brett Baer from SSAB for his help on this posts technical information.
Check out our previous post on which welding method is truly the best: