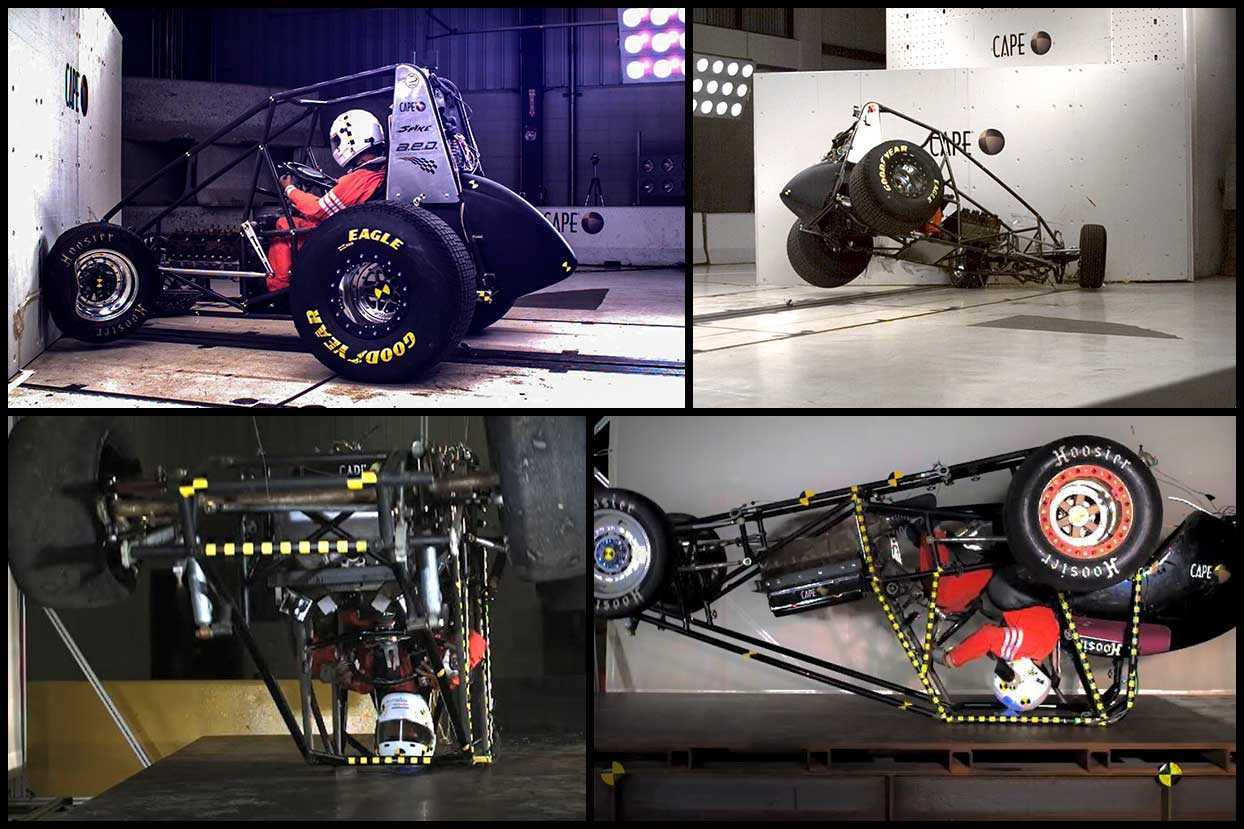
Several years ago, A.E.D., partnering with Spike Chassis and CAPE – The Center for Advanced Product Evaluation, set out to crash test a sprint car to provide real world scenarios of what happens during an extreme sprint car crash.
A.E.D., Spike and CAPE performed 3 separate crash tests and a drop test on three different chassis. Spike Chassis built three cars with 4130 chrome moly (chromoly) tube supplied by A.E.D., and produced by Webco Industries (USA).
These tests have allowed us to collect data and analyze many different details such as the chassis upper roll cage structure, impact values, how 4130 holds up under these extreme crash conditions, and how the human body responds and stretches under these types of loads. The data collected has also been used to perform further testing on design and different materials used in building of chassis in simulators, as well as creating stepping stones for numerous academic programs to study structures and safety engineering.
First Sprint Car Chassis Crash Test
The first chassis was subjected to a front-end impact followed by an impact to the halo. A dual crash test was performed because many times after a front impact, a sprint car tends to roll and flip into the air, often 10 feet or higher, and then makes impact or multiple impacts with barriers, the ground and/or other cars. While the second impact test may have been aggressive, it presented information certainly of interest to chassis builders and drivers alike.
The second chassis was subjected to an impact to the halo and was used to review that data against the first two tests. This chassis was built with slight modifications to the wall thickness of the upper halo tubes. Upon review we did not note any significant changes to the compression of the cage.
Sprint Car Chassis Drop Test
The last test was a drop test on a third sprint car chassis. This chassis was lifted upside down to a height of 12 feet and then dropped onto a steel plate to create impact on the halo of the car. This sprint car was built to USAC specs with a driver’s head clearance of approximately 3.75” from the top halo tubes. A brand-new set of SFI approved belts was used and properly mounted and laced to SFI standards.
Further testing by IUPUI
Further testing was done by researchers at IUPUI in advanced simulators using the data collected from these crash tests. The simulations included tests conducted on Midgets under these conditions:
(a) one built to current design and specs of cars being raced,
(b) a car with a stiffened cage and chassis with an additional halo structure added,
(c) one with the original chassis and added roll hoops to cage and
(d) one with the original chassis design with additional halo structures.
IUPUI concluded from these tests that (d), the original chassis with the additional halo structure, was the best design. It is important to note that the simulation did not take into consideration the “heat affected zones” caused by the manufacturing process. You can purchase the full report directly from SAE.org.
What have we learned?
All the parties involved in these 4 tests gained some valuable information from the data collected. Some of this data has been used to improve current chassis designs. At A.E.D., we specifically learned a lot about the performance of our 4130 tube produced by Webco industries. The front-end impact showed that the 4130 tube was able to absorb the impact and not affect the cage structure of the chassis.
The major messages we received from these tests were that the current rules for minimum distance of the helmet to the halo should be significantly increased; and seats, padding, etc. should be adjusted accordingly per driver. It was observed when the drop test was performed that when the car was held upside down on a rotisserie, the crash dummy stretched nearly 2 inches in a static position. All three impacts to the halo of the car resulted in the dummy’s helmet contacting the barrier or steel plate. During the drop test, the dummy’s helmet made contact more than once as the car bounced off the steel plate. At this point in time, no definitive solution has been made to increase driver protection in this regard, although in the years following these tests, we have seen more chassis with additional halo structures and increased head clearance for drivers. While it has been noted that a couple of chassis manufacturers were exploring additional halo structures during and around the time of these tests, a number of mini sprint builders lead the idea with their cars. This positively influenced others and various levels of open wheel racing to explore and offer similar upgrades to improve safety.